A Plastic Recycling Granulation Machine is a type of equipment used to process waste or scrap plastic into reusable plastic granules. It melts down used plastic materials like PE, PP, or PET and reshapes them into small, uniform pellets through extrusion and cutting.
This machine plays a key role in plastic recycling by turning discarded plastics into raw materials for new products. It helps reduce plastic pollution, lowers production costs, and supports sustainable manufacturing across industries like packaging, construction, and consumer goods.
Understanding the features, pros and cons, and possible applications of the Plastic Recycling Granulation Machine will help you make better decisions and choose the right granulator or combination to meet your manufacturing needs.
Read on as we detail several different Plastic Recycling Granulation Machines and provide a short guide at the end of the article to choose the best granulator for your project.
Types of Plastic Recycling Granulation Machine
Modern Plastic Recycling Granulation Machines are designed with energy-efficient systems, automatic temperature control, and advanced filtration to ensure high-quality granules. They are widely used in recycling plants, plastic product factories, and environmental processing centers to handle a wide range of plastic waste, from film and bottles to injection-molded parts.
Next, we will briefly discuss the 12 different types of granulators.
1. Recycling compactor granulation line
A Recycling Compactor Granulation Line is a complete system used to process lightweight plastic waste—such as films, woven bags, and foamed materials—into dense plastic pellets. It combines compaction, extrusion, filtration, and pelletizing into one continuous process. The compactor pre-compresses soft or bulky materials, making them easier to feed into the extruder without bridging or clogging.
Advantages
Efficient Feeding: The built-in compactor pre-processes light and fluffy materials, preventing feeding blockages.
Integrated System: Combines compaction, extrusion, filtration, and pelletizing in one continuous line.
Space & Labor Saving: Compact design with high automation reduces the need for manual labor and factory space.
Wide Material Compatibility: Handles various soft plastics like PE/PP film, woven bags, and foam materials.
Consistent Pellet Quality: Produces uniform plastic granules suitable for reuse in production.
Disadvantages
Not Suitable for Hard Plastics: Thick or rigid plastics (e.g., injection-molded parts, bottles) may require other machines.
Material Cleanliness Required: High moisture or contamination levels (like dirt or paper) can affect performance and pellet quality.
Regular Maintenance Needed: The compactor and filtration areas require periodic cleaning to ensure stable operation.
Applications
Agricultural Film Recycling: For PE mulch film, greenhouse film, and other farm waste plastics.
Post-Consumer Plastic Packaging: Ideal for processing shopping bags, stretch film, courier bags, etc.
Industrial Scrap Recovery: Recycles production waste from film and woven bag manufacturers.
Plastic Recycling Plants: Best suited for facilities handling large volumes of soft plastic waste.
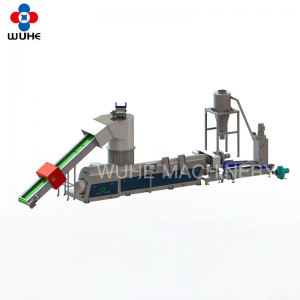
2. Crushed material granulation line
A Crushed Material Granulation Line is a plastic recycling system designed to process hard plastic waste that has already been shredded or crushed into flakes. This includes materials like HDPE, PP, PET, ABS, or PC from bottles, containers, and industrial scraps. The line typically includes a feeding system, single or twin-screw extruder, filtration unit, pelletizing system, and cooling/drying section.
Advantages
Direct Feeding of Crushed Materials: No need for pre-compaction; suitable for rigid plastics like bottles, containers, and injection parts.
Stable Output: Works well with uniform, dense materials, providing consistent extrusion and pellet quality.
High Efficiency: Strong screw design and efficient degassing system improve melting and reduce moisture issues.
Flexible Configuration: Can be equipped with single or twin-stage extruders, water-ring or strand pelletizers based on material type.
Good for Clean Regrind: Especially effective when processing clean, sorted plastic flakes from washing lines.
Disadvantages
Not Ideal for Soft or Fluffy Plastics: Light materials like films or foams may cause feeding instability or bridging.
Requires pre-washing: Dirty or contaminated crushed materials need thorough cleaning before granulation.
Less Suitable for Mixed Plastics: Material consistency affects pellet quality; mixed polymer types may require blending or separation.
Applications
Rigid Plastic Recycling: For HDPE/PP bottles, shampoo containers, detergent barrels, etc.
Post-Industrial Plastic Scrap: Suitable for crushed leftovers from injection molding, extrusion, or blow molding.
Washed Flakes from Recycling Lines: Works well with cleaned PET, PE, or PP flakes from bottle washing systems.
Plastic Pellet Producers: Ideal for manufacturers converting clean regrind into reusable pellets for injection or extrusion.
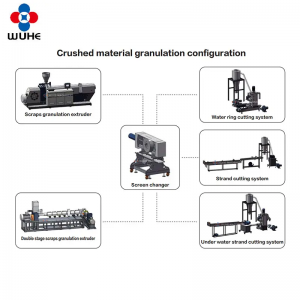
3. Woven fabric bag recycling pelletizing line
A Woven Fabric Bag Recycling Pelletizing Line is a specialized recycling system designed to process PP (polypropylene) woven bags, raffia, jumbo bags (FIBCs), and other similar plastic textiles. These materials are typically lightweight, tear-resistant, and difficult to feed directly into traditional pelletizing systems due to their bulky structure. This line combines crushing, compacting, extrusion, filtration, and pelletizing into a continuous process that converts used woven plastic materials into uniform plastic pellets.
This solution is ideal for recycling post-industrial and post-consumer woven packaging waste, helping reduce environmental pollution and regenerating raw materials for the plastic industry.
Advantages
Integrated Compactor System: Effectively compresses lightweight, woven materials to ensure smooth and stable feeding into the extruder.
High Efficiency: Designed for high-capacity processing with continuous operation and low manpower requirements.
Durable and Stable Output: Produces uniform pellets with good mechanical properties, suitable for downstream reuse.
Handles Challenging Materials: Specifically built to handle woven bags, jumbo bags with liners, and raffia waste.
Customizable Design: Configurable with various cutting, degassing, and filtration systems tailored to different material conditions.
Disadvantages
Pre-treatment Often Needed: Dirty woven bags may require washing and drying before recycling to maintain pellet quality.
High Energy Consumption: Due to the compacting and melting of dense materials, the system can consume more power.
Material Sensitivity: Inconsistent material thickness or leftover sewing threads may affect feeding and extrusion stability.
Applications
Recycling PP Woven Sacks: Ideal for cement bags, rice sacks, sugar bags, and animal feed bags.
Jumbo Bag (FIBC) Reprocessing: An Efficient solution for recycling large flexible intermediate bulk containers.
Textile and Raffia Waste Recycling: Suitable for manufacturers of woven textiles and raffia products to recycle edge trim and scrap.
Plastic Pellet Production: Produces high-quality PP granules for reuse in injection molding, extrusion, or film blowing.
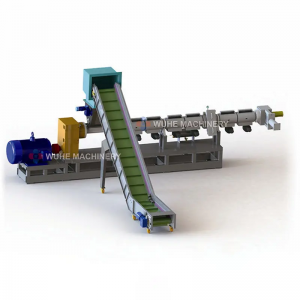
4.EPS/XPS Granulation Line
An EPS/XPS Granulation Line is a specialized recycling system designed to process expanded polystyrene (EPS) and extruded polystyrene (XPS) foam waste into reusable plastic granules. EPS and XPS are lightweight, foamed materials commonly used in packaging, insulation, and construction. Due to their bulky nature and low density, they are difficult to handle using conventional plastic recycling equipment. This granulation line typically includes crushing, compacting (melting or densifying), extrusion, filtration, and pelletizing systems.
The main purpose of this line is to reduce volume, melt, and reprocess EPS/XPS foam waste into uniform polystyrene pellets (GPPS or HIPS), which can be used again in plastic manufacturing.
Advantages
Volume Reduction: The compactor or densifier system significantly reduces the volume of foam materials, improving feeding efficiency.
High Output with Light Materials: Specially designed for low-density foam, ensuring stable feeding and continuous extrusion.
Energy-Saving Screw Design: Optimized screw and barrel structure ensures efficient melting with reduced energy consumption.
Environmentally Friendly: Helps reduce landfill waste and supports circular use of foam packaging and insulation materials.
Recyclable Output: The granules produced are suitable for reuse in non-food applications like insulation sheets or plastic profiles.
Disadvantages
Requires Clean and Dry Foam: EPS/XPS must be free from oil, food, or heavy contamination to maintain pellet quality.
Odor and Fume Control Needed: Melting foam may release fumes; proper ventilation or exhaust systems are essential.
Not Suitable for Mixed Plastics: The system is optimized for pure EPS/XPS; mixed materials may clog or degrade output quality.
Applications
Packaging Foam Recycling: Ideal for recycling white EPS packaging used in electronics, appliances, and furniture.
Construction Material Recovery: Suitable for XPS board scrap from building insulation and wall panels.
Foam Factory Waste Management: Used by EPS/XPS product manufacturers to recycle production edge trim and rejected pieces.
Polystyrene Pellet Production: Converts foam waste into GPPS/HIPS granules for downstream applications such as plastic sheets, hangers, or molded products.
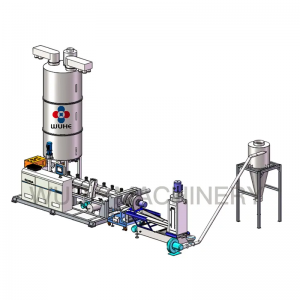
5. Parallel Twin Screw Granulation Line
A Parallel Twin Screw Granulation Line is a plastic processing system that uses two parallel intermeshing screws to melt, mix, and pelletize various plastic materials. Compared to single screw extruders, twin screws provide better mixing, higher output, and greater control over processing conditions. This system is especially suitable for recycling mixed plastics, compounding additives, and producing high-quality plastic granules with improved properties.
The line generally consists of a feeding system, parallel twin screw extruder, filtration unit, pelletizer, and cooling/drying section, designed for continuous and stable operation.
Advantages
Superior Mixing and Compounding: Twin screws offer excellent homogenization, allowing for blending of different polymers and additives.
High Throughput and Efficiency: Provides higher output and better processing stability compared to single screw extruders.
Versatile Material Handling: Suitable for processing a wide range of plastics, including PVC, PE, PP, ABS, and recycled mixed plastics.
Enhanced Process Control: Independent screw speed and temperature zones allow precise adjustment for optimal pellet quality.
Improved Degassing: Efficient removal of moisture and volatiles, resulting in cleaner pellets.
Disadvantages
Higher Initial Investment: Twin screw systems are generally more expensive to purchase and maintain than single screw extruders.
Complex Operation and Maintenance: Requires skilled operators and regular maintenance to keep screws and barrels in good condition.
Not Ideal for Very High-Viscosity Materials: Some extremely viscous materials may require specialized equipment or processing conditions.
Applications
Plastic Recycling: Effective for reprocessing mixed plastic waste into uniform granules for reuse.
Compounding and Masterbatch Production: Widely used in producing plastic compounds with fillers, colorants, or additives.
PVC and Engineering Plastics Processing: Ideal for handling heat-sensitive and complex polymers.
High-Performance Material Manufacturing: Used in producing specialty plastics with tailored mechanical or chemical properties.
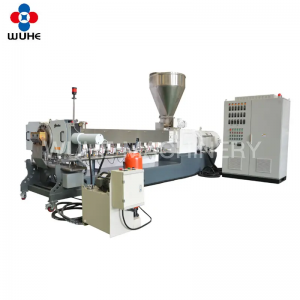
Key Points for Selecting the Best Plastic Recycling Granulation Machine Type
The following are some critical considerations for Plastic Recycling Granulation Machine selection that can fulfill your manufacturing needs.
1. Know Your Material Type
Soft Plastics (e.g., film, bags, foam): Choose a machine with a compactor or densifier to ensure smooth feeding.
Hard Plastics (e.g., bottles, rigid containers): A crushed material granulation line with stable feeding is more suitable.
Mixed or Contaminated Plastics: Consider twin screw extruders with strong mixing and filtration capabilities.
2. Assess Output Capacity Needs
Estimate your daily or monthly processing volume.
Choose a model that matches your desired throughput (kg/h or tons/day) to avoid under- or over-sizing.
For large-scale recycling, high-output twin-screw or double-stage systems are ideal.
3. Check for Feeding & Pre-treatment Requirements
Does your material need washing, drying, or crushing before granulation?
Some machines include integrated shredders, washers, or compactors. Others require external equipment.
Dirty or wet materials require strong degas systems and melt filtration.
4. Consider Final Pellet Quality
For high-end applications (e.g. film blowing, injection molding), consistent pellet size and purity matter.
Machines with precise temperature control and automatic screen changers produce cleaner, more uniform granules.
5. Energy Efficiency & Automation
Look for machines with inverter-controlled motors, energy-saving heaters, and PLC automation.
Automated systems reduce labor costs and ensure consistent production quality.
6. Maintenance & Spare Parts Support
Choose a machine from a reliable supplier with fast-response service, technical support, and easy-access spare parts.
Simpler designs may reduce downtime and lower long-term maintenance costs.
7. Customization & Future Expansion
Consider machines with modular designs that allow upgrades (e.g., adding a second extruder or changing pelletizing type).
A flexible system adapts to new material types or higher output as your business grows.
Consider WUHE MACHINERY’s Plastic Recycling Granulation Machine Service
As a professional manufacturer with over 20 years of experience, WUHE MACHINERY (Zhangjiagang Wuhe Machinery Co., Ltd.) excels in the design, production, and global service of plastic recycling granulation machines.
With more than 500 systems installed and over 1 million tons of plastic processed annually—reducing an estimated 360,000 tons of CO₂ emissions—WUHE has proven its technical capability and environmental impact.
Backed by ISO 9001 and CE certifications, they offer integrated solutions for film, woven bag, EPS/XPS, crushed plastic, and twin‑screw granulation lines. Their strict quality control, modular system design, OEM/ODM flexibility, and responsive after‑sales support ensure that B2B buyers receive reliable, high-efficiency, and tailored recycling solutions worldwide.
Choose WUHE MACHINERY for reliable performance, customized recycling solutions, and a trusted partner in building a greener, more sustainable plastics industry.
Post time: Jul-01-2025